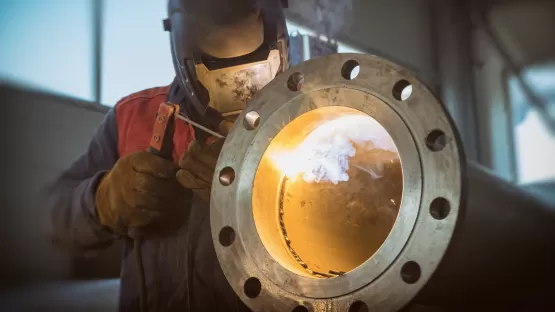
De belangrijkste lasfouten
Vaak krijgen lassers te maken met defecten in gelaste verbindingen en moeten ze die verhelpen. Deze gebreken zijn niet altijd gemakkelijk in één oogopslag te ontdekken. Air Liquide, specialist in lasprocessen en beschermgassen, legt in detail uit wat de belangrijkste defecten zijn bij het lassen van metaal, en hoe je die in de werkplaats kunt vermijden.
Het lassen van metalen
In het algemeen zijn de meeste metalen lasbaar op TIG / MIG / MAG of laser machines, met verschillende niveaus van metallurgische of operationele moeilijkheid.
De verschillende soorten staal
Volgende staalsoorten kunnen gelast worden, mits de nodige aandachtspunten:
- Ongelegeerd staal of koolstofstaal
- Laag gelegeerd staal
- Austenitisch roestvast staal
- Ferritisch, duplex en martensitisch roestvast staal
Elke van deze staalsoorten gedraagt zich anders, sommige legeringen binnen deze groepen kunnen ook specifieke eigenschappen hebben die een invloed hebben op de lasbaarheid.
De belangrijkste lasfouten
We kunnen lasfouten in twee categorieën indelen: die welke te maken hebben met het proces of de werkingsparameters, en de metallurgische defecten.
-
Warmscheuren
Temperatuurstijgingen tijdens het lassen veroorzaken thermische uitzetting, wat mechanische spanningen tot gevolg heeft als een onderdeel niet vrij kan uitzetten en krimpen. Afhankelijk van de warmte-inbreng, de hoogte/breedte verhouding van de lasdoorsneden en de samenstelling van het lasmetaal kan de lasnaad over de langsrichting scheuren.
-
Porositeiten / blowouts
Afhankelijk van het materiaal kunnen er porositeiten of blaasgaten (blowouts) in de lasrups verschijnen. Vloeibaar lasmetaal in het smeltbad lost gassen op tijdens het lassen. Aangezien de oplosbaarheidsgrens van vast metaal vele malen lager ligt dan die van vloeibaar metaal, zullen deze gassen tijdens het stollen ontsnappen uit de lasverbinding. Wanneer dit onvoldoende mogelijk is (vb. door een snelle stolling of door een grote hoeveelheid opgelost gas) dan kunnen zich bellen vormen en wordt de lasnaad poreus.
Bijvoorbeeld:
- Koolstofstaal verdraagt slechts zeer kleine hoeveelheden stikstof.
- Aluminium met waterstof (dat kan komen van vocht in de lucht of van de aluminiumoxide huid)
Opgemerkt moet worden dat de toepassing van het beschermgas een belangrijke rol speelt bij het voorkomen van het ontstaan van porositeiten. Vaak gaat het minder om de zuiverheid van het gas dan wel om de stand van de toorts, de afstelling van het gasdebiet enz. Ook de oppervlaktevoorbereiding is belangrijk.
-
Geometrische onvolkomenheden
Als deze keuze van de belangrijkste lasparameters gemaakt is, moet de geometrie van de lasrups geoptimaliseerd worden.
Speciale aandacht moet worden besteed aan:
- Inbranding: maximale diepte van het gesmolten gebied. Net voldoende en zonder gevaar op doorbranden. Bij sommige procédés worden onderlegstrips gebruikt om een goede inbranding te garanderen. Ze kunnen gemaakt zijn van watergekoeld koper of van keramisch materiaal.
- De vorm van inbranding: voor hoeklassen bijvoorbeeld is de zogenaamde "vingervormige inbranding" synoniem met het risico van gebrek aan inbranding van de wortel
- Overdikte: overtollige dikte moet beperkt worden, in samenhang met de geldende eisen, om de lassnelheid en de productiviteit te optimaliseren.
- Lasuiterlijk: de aanvloeiing moet zo goed mogelijk zijn. Bij verbindingen die aan vermoeiing onderhevig zijn, zullen slecht aangevloeide lasnaden voor spanningsconcentraties zorgen met een falende verbinding tot gevolg.
- Randinkarteling: verschijnt soms aan de rand van de lasrups, wat vaak te maken heeft met een te hoge lassnelheid of een verkeerde instelling van de elektrische spanning.
Er bestaat meetgereedschap om deze onvolkomenheden te meten en te beoordelen t.o.v. de acceptatiecriteria van een gelaste constructie.
-
Koudscheuren
Koudscheurvorming kan in sommige materialen kunnen ontstaan, enkele dagen na het lassen, vaak als het onderdeel onder spanning staat of in werking is.
Het principe is vrij ingewikkeld: afhankelijk van de materialen (staal, ferritisch roestvast staal bijvoorbeeld) kan bij de lassen zogenaamde diffundeerbare waterstof in de metaalmatrix ingebracht worden. Deze waterstofatomen zullen tijdens de belasting van de verbinding geleidelijk naar de korrelgrens van de structuur migreren en breuken initiëren. Het is daarom bijzonder belangrijk de gevoeligheid van een materiaal voor koudscheuren te controleren alvorens te lassen om de nodige maatregelen te kunnen nemen.
-
Verandering van mechanische eigenschappen
De optimale draad-gas combinaties moeten gekozen worden om de mechanische eigenschappen van een gelaste verbinding te garanderen. De effecten van een verhoogde opgeloste zuurstofconcentratie of een slechte overdracht van legeringselementen in de boog kunnen bij booglassen aanzienlijk zijn.
Ook bij het lassen van austenitisch roestvast staal ontstaan door overmatige oxidatie chroomcarbiden die de corrosiebestendigheid kunnen aantasten.
De elektrische parameters stroom/spanning kunnen de korrelgrootte bij het stollen en in de warmte-beïnvloede zone beïnvloeden en de mechanische eigenschappen sterk verslechteren.
-
Lasuiterlijk
Er zijn veel parameters die het uiterlijk van de lasrups en dus de kwaliteit kunnen veranderen. Deze omvatten onder meer:
- Roestvrij stalen lasrupsen verkleuren door oxidatie wanneer ze te warm worden gelast of te snel worden blootgesteld aan de omgevingslucht na het lassen.
- Silicaten: meestal in de vorm van eilandjes aan het oppervlak van de lasnaad. Ze kunnen defecten veroorzaken bij het lassen in meerdere lagen of na het conserveren (vb. verf) latere problemen geven (spalling).
Ook hier is de keuze van het draad/gas combinatie belangrijk.
Houd bij het lassen, solderen en snijden rekening met de beschikbare persoonlijke beschermingsmiddelen, zoals lashelmen, werkhandschoenen, de juiste kleding en gereedschappen.
Ontdek onze oplossingen
Heb je vragen over de belangrijkste lasfouten? Vul ons contactformulier in.
Onze experts reageren binnen 24 uur.Vaak gestelde vragen
Hoe las je gegalvaniseerd staal?
Hoe roestvrij staal te lassen?
Hoe kies je het gas dat je in MIG of MAG gebruikt?
Hoe kies je welk gas je in TIG of Plasma gebruikt?
Hoe voorkom je overconsumptie van lasgas?
Waarom een gevulde draad gebruiken?
Hoe pas je de gasstroom aan bij het lassen?
Wat is het verschil tussen solderen en solderen?